Call this an ERP horror story
Let me tell you about a sad, frightening world.
In this world, a small aerospace company nearly went bankrupt after implementing a promising IT system. A window manufacturer spent eight years, €10+ million and an incredible amount of energy to implement a new IT system in two (!) of its 15 production sites. Meanwhile, a food company maintains 13 equivalent, different systems across its manufacturing infrastructure.
In this world, 60% of digital IT projects fail.
I would like to tell you this is a science fiction world, but unfortunately, this is the reality of Enterprise Resource Planning systems in factories.
Over the past 30 years, ERP systems have become the go-to project management solution for manufacturers to control costs and manage supply chains and production. And why not? ERPs are a central IT solution that generated tons of savings and revolutionized an industrial world which habitually siloed its activities.
Sounds magical, right? And it was… when it landed in manufacturing 30 years ago. But the demands placed on manufacturers today have created an environment where adapting to change is more important than executing a plan.
The Big Bad, the Redeemable Bad, and… No good to be found
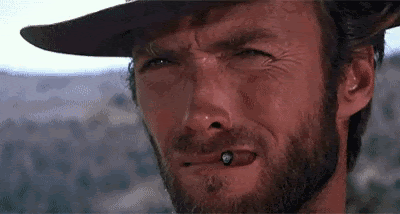
In our current world, where ERP still dominates IT solutions in factories, we find three actors.
First we have ERP, aka The Big Bad. These systems hold clients captive. There’s no interest for ERP providers in improving their offerings overall, because each improvement requested by a client means big bucks for them. So they serve a product so general, it might as well be called medicare, and profit from the customizations companies need to even approach a robust ERP solution. This business model results in a maximum Net Promoter Score of 10/100.
Then you’ve got the second actor, normally the CIO or CFO, aka the Redeemable Bad. These guys are unconsciously bad because they have a narrow focus, generally on achieving an optimal financial result or freedom from the daily need to code or manage data. They are redeemable because they have the power to break out of the prison ERP created.
Finally, we have our third actor, the end user, aka the Neglected. This person actually interacts with the system for their daily activities: production planning, quality assurance, procurement, workload balancing. Ironically, no one consults the end user when choosing and implementing a new system, hence their moniker, the Neglected.
As for the good, there’s no room for it in the current approach to factory IT. That’s why when it comes to ERP, it’s time to say…
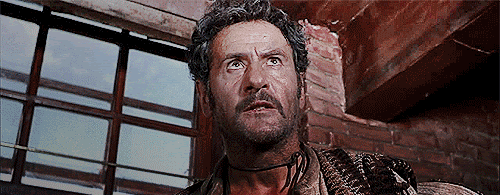
Not convinced? There must be some good somewhere, you say?
Please, read on.
ERP in practice today
When assessing the IT system performance of a client in the luxury sector, we interviewed the CIO about their approach. After a few minutes, he came to an unbelievable conclusion: “Maybe we should go to see the final users, we never do that!”
In this CIO’s company, more than 100 FTE were dedicated to supporting the SAP system. But management had never gone to the shopfloor to understand how the final user interacts with the application functionalities and interface.
Not too long after that, I was on the shopfloor of a food manufacturing company. The CEO had decided to implement a new ERP, and it had just gone live. I spent two hours in the milk production area shadowing a worker who monitored the quality of the milk batches after they’d been transferred into the factory’s tanks.
I’ve never met a more patient person in my life. He tested 50 samples over eight hours. Every time he sampled the milk, he entered the same parameters in three different screens. Then he copied the same information on a sheet of paper, which he photographed with his personal phone (the company did not provide one). Finally, he went into a separate room to enter the information into another part of the system.
Finally, I had to ask him what he thought about this process.
“My boss told me it’s normal,” he replied. “This should improve someday.”
An ever-growing technical debt
When you commit to a new ERP, you have two choices. Either you adapt your processes to the system, forcing you to sacrifice some of the functionalities, or you customize the software. Customizing ERP is a pain in the butt two times over, though. In the short run, you have to hire expensive expert consultants, and in the long run, possibly before you even get your original ERP software to a customized version, you’ll need to spend even more money to upgrade.
In fact, studies indicate that if a company doesn’t innovate technically, its IT system will accumulate a technical debt of 20-25% per year. So after four years, your ERP system will become fully obsolete, unless you attempt to keep technical debt low by upgrading at the following rate.
- Year One: Implement an update
- Year Two: Finish implementation and debug
- Year Three: Enjoy your system as much as you can (assuming nothing has gone wrong in years one and two)
- Year Four: Begin again
Keeping this schedule is highly unrealistic, as evidenced by the fact that a majority of companies are two versions behind an ERP company’s latest offering.
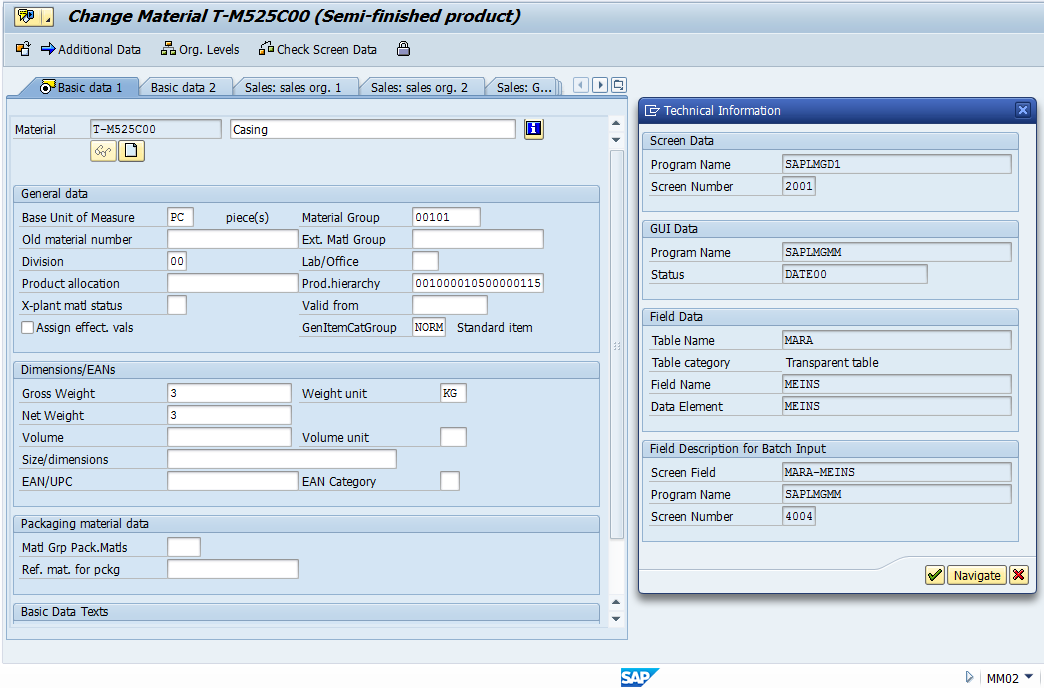
ERP: Anything But Agile
Let’s take a look at how a typical ERP implementation goes. The typical approach to project management for a tech company is the agile method, which has become as natural to tech companies as brushing their teeth. But manufacturing has not yet entered this new age of project management. Instead, when manufacturers launch an ERP implementation, they use the “V cycle” method.
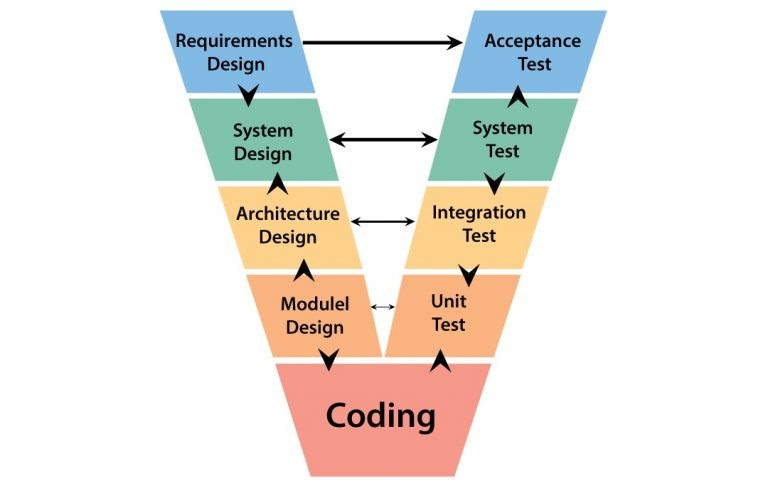
The V cycle lasts about two years, and is a long and complex process that will supposedly result in a perfect result, and which never does. Not only that, but the average extra cost of such projects is 27%, and the grand majority (85%) are late.
But it makes for such a pretty picture! Why does it fail to deliver?
Improper project management is a key issue. Middle management discovers the ERP’s key functionalities too late, top management deems the project “IT only,” and transversal communication is generally inadequate, resulting in a major failure of interfaces. As for the final user, they are consulted, if they are at all, at the end of the process, when it is too late to integrate their feedback.
Secondly, ERP implementation neglects data architecture, meaning that companies cannot utilize “plug and play” applications for agile customizations to manufacturer’s needs. Eventually, this lack of an agile data architecture results in barriers to important technologies like machine learning, artificial intelligence, and blockchain, simply because companies can’t implement them in conjunction with ERP systems.
Also impossible to implement? Customization.
Manufacturers regard ERP as a global solution to all their IT needs, which prevents companies from separating the essential functions that could remain in ERP and functions in need of a different solution. Viewing ERP as the end-all, be-all for IT results in a damaging mindset gap where companies reject agile software’s ugly baby approach, where IT solutions are implemented as soon as they are viable and improved with use, in favor of the V cycle’s perfectionist approach, which focuses on delivering a set of features as agreed upon by top management and a vendor. But this method of trying to fit a square peg in a round hole, i.e. making ERP a solution for every single IT need, results in lost time because of inefficient use of solutions like Excel, or wasted money because of expensive (often inadequate) ERP add-ons. And meanwhile, SaaS or low code/no code solutions that can solve manufacturing blockages or improve processes in a highly efficient, customized manner, are thrown to the side.
Four key steps to bring agility to a factory
Already, 5% of manufacturing companies have moved to a data-centric view of ERP implementation. These companies have a tremendous competitive advantage because technological transformation has prepared them for the next cycle of innovation in manufacturing: machine learning, edge computing, artificial intelligence. Such innovation leads to opportunities in prediction (sales, maintenance, quality), real-time management (delivery, production), fast and informed decision making (which leads to global benefits), and product “as a service” and other new business models.
Putting agile softwares in place of ERP functionalities requires manufacturers to take a few key steps.
- Free themselves from big vendors.
- Manage IT with a horizontal view that takes end users into account from day one.
- Accept the “test and learn” nature of agile workflows.
- Design a diverse, agile, and robust IT architecture with actually optimized solutions and data integration.
Companies held captive by ERP softwares are truly in danger due to their outdated IT solutions. But, people with ropes around their neck don’t always hang. Now is the time to take control of the IT solutions in your factory so you can join those leaders in the top 5%, and stop eating their dust.